In this blog, you will learn step by step about the manual design of a two way slab for one floor of the G + 5 building procedure using I.S. 456:2000. For daily blogs, subscribe to our blog page and learn complete information about the structural engineering industry
Steps :-

Given :-
1) Grade of Concrete = M20
2) Grade of Steel = Fe500
3) Clear Cover to Reinforcement (c) = 20 mm
4) Dimension of Slab = (3050mm X 4180 mm)
5) Assume Beam Support (Bearing) = 230 mm
6) Unit Weight of Concrete = 25 kN/m2
Step 1 :- Aspect Ratio (Refer Cl. No. D-1.11, Page No. 90 , I.S. 456:2000)
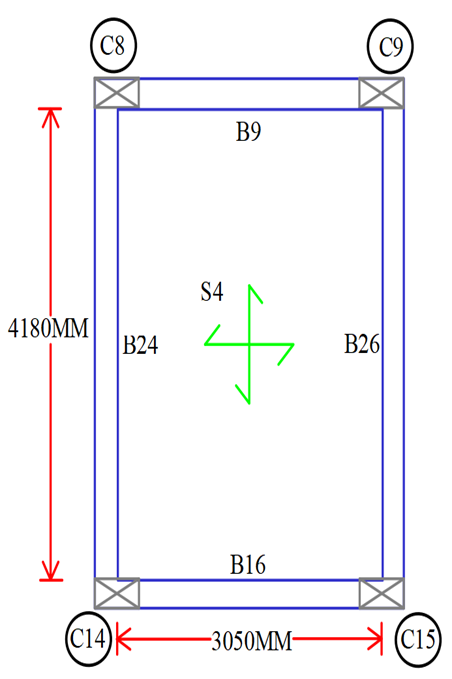
Lx = 3050 mm & Ly = 4180 mm …(Given)
Therefore, Ly/Lx = 4180/3050 = 1.37 < 2 …(Two Way Slab)

Step 2 :- Depth of Slab (D)
Basic Value (B.V.) = L / D = 26
Assume % of Steel = 0.25 %
Therefore, Modification Factor (M.F.) = 1.35 …(Refer Fig. 4 , Page No. 38 , I.S.456:2000)
Therefore, Effective Depth (d) = SPAN/B.V.X.M.F = [3050 / (26 X 1.35)] = 86.894 mm
Assume Bars to be Provided of Diameter = 8 mm & Provide Clear Cover to Reinforcement = 20 mm
Therefore, Overall Depth of Slab (D) = d + c + (8/2) = 86.894 + 20 + 4 = 110.894 ≈ 125 mm
Therefore, Effective Depth Provided (dprovided) = D – c – (8/2) = 125 – 20 – 4 = 101 mm
Step 3 :- Effective Span (le)
Minimum of, i) Le = Lx + Bearing = 3050 + 230 = 3280 mm
ii) Le = Lx + d = 3050 + 101 = 3151 mm
Therefore, Effective Span (Le) = 3151 mm
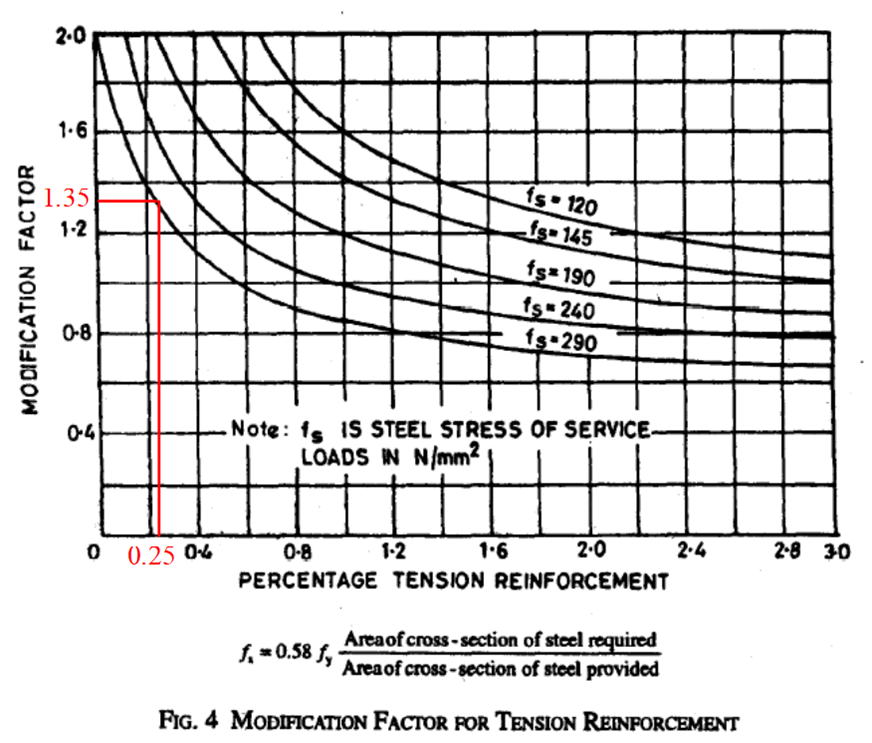
Step 4 :- Load Calculations
Consider 1 m Strip of Slab,
i) Self Weight of Slab (DL) = D X Unit Weight of Concrete
= 0.125 X 25
= 3.125 kN/m2
ii) Live Load (LL) = 2 kN/m2 …[Refer Table No. 1 , Page No. 7 , I.S. 875 (Part 2) : 1987]
iii) Super Imposed Dead Load (SIDL) =
Floor Finish = Wt. of Screeding (50 mm Thk.) + Flooring (10 mm Thk.)
= (0.05 X 24) + (0.01 X 22) …[Refer I.S. 875 (Part 1) : 1987]
= 1.42 kN/m2
≈ 1.5 kN/m2
Total Load (W) = 3.125 + 2 + 1.5
= 6.625 kN/m2
≈ 6.63 kN/m2
Total Ultimate Load (Wu) = 6.63 X 1.5
= 9.945 kN/m2
≈ 9.95 kN/m2
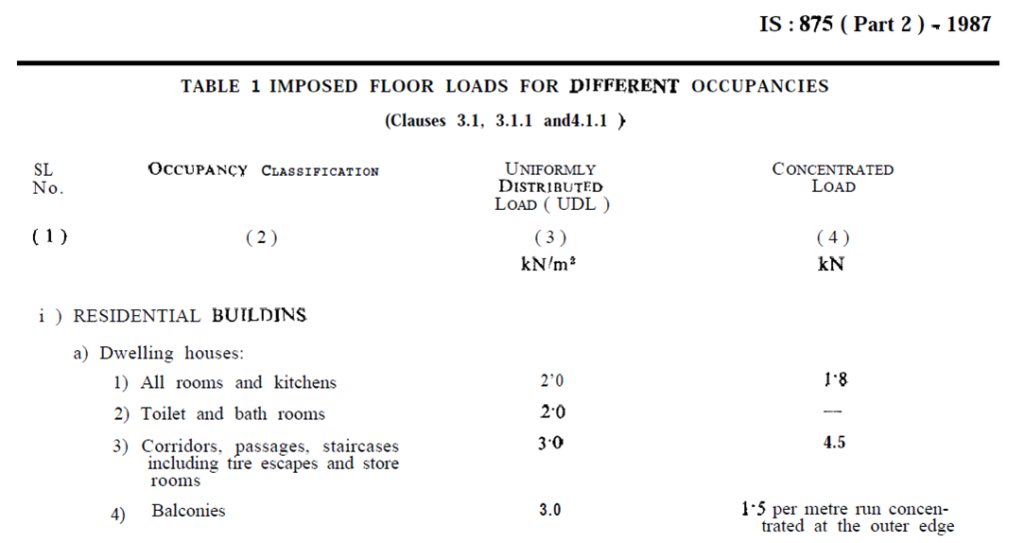
Step 5 :- Maximum Design Bending Moment (Mumax)
Ly/Lx | |||
1.3 | 1.37 | 1.4 | |
-αx | 0.065 | ? | 0.071 |
+αx | 0.049 | ? | 0.053 |
Shorter Span Moments :-
1) -ve Moment at Continuous Edge :-
By Interpolation,
-αx = 0.065+[{(0.071-0.065) / (1.4-1.3)} X (1.37 – 1.3)]
= 0.0692
Mu = -αx . Wu . le2
= 0.0692 X 9.95 X 3.1512
= 6.836 kN.m
2) +ve Moment at Mid-Span :-
By Interpolation,
+αx = 0.049+[{(0.053-0.049) / (1.4-1.3)} X (1.37 – 1.3)]
= 0.0518
Mu = +αx . Wu . le2
= 0.0518 X 9.95 X 3.1512
= 5.117 kN.m
Longer Span Moments :-
3) -ve Moment at Continuous Edge :-
Mu = -αy . Wu . le2
= 0.047 X 9.95 X 3.1512
= 4.64 kN.m
4) +ve Moment at Mid-Span :-
Mu = +αy . Wu . le2
= 0.035 X 9.95 X 3.1512
= 3.46 kN.m
Therefore, Maximum Design Bending Moment (Mumax) = 6.836 kN.m
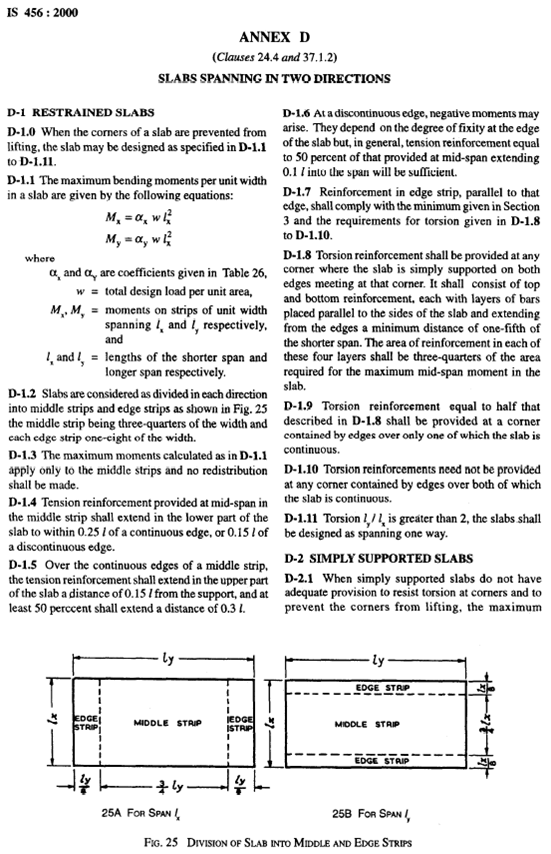
Step 6 :- Check For Depth
Equate Mumax & Mulim,
Mumax = Mulim
6.836 X 106 = 0.133 X fck X b X dreq2
6.836 X 106 = 0.133 X 20 X 1000 X dreq2
dreq= 50.7 mm < 101 mm …(dreq< dprovided)
Therefore, Safe
Step 7 :- Area of Steel Calculation :-
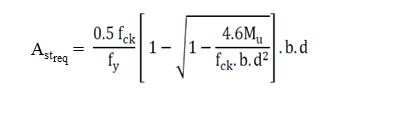
Spacing of Bars :-
As per Cl. No. 26.3.3 (b) , Page No. 46 , I.S. 456 : 2000
Maximum Spacing
Between Bars < Minimum of i) 3d
ii) 300 mm
Therefore,
Maximum Spacing Between Bars = i) 3 X 101 = 303 mm
ii) 300 mm
Note:- Generally We Provide 200 mm Maximum Spacing Between Bars.
Spacing of Bars = Area of one bar/ Area of steel * 1000
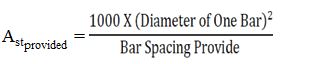
Along Shorter Span (Lx) :-
1) At Support :-

= 162.18 mm2
Spacing of Bars = (Area of One Bar / Area of Steel) . 1000
Consider Bars to Provide are of Diameter 8mm.
Therefore, Spacing of Bars = [(π/4) X 82 / 162.18] X 1000 = 3709.98 mm
Note:- Generally We Provide 200 mm Maximum Spacing Between Bars.

2) At Mid-Span :-

= 120.1 mm2
Spacing of Bars = (Area of One Bar / Area of Steel) . 1000
Consider Bars to be Provide are of Diameter 8mm.
Therefore, Spacing of Bars = [(π/4) X 82 / 120.1 ] X 1000 = 418.58 mm
Note:- Generally We Provide 200 mm Maximum Spacing Between Bars.

Along Longer Span (Ly) :-
d = dprovided – diameter of bar provided along shorter span = 101 – 8 = 93 mm
1) At Support :-

= 118.53 mm2
Spacing of Bars = (Area of One Bar / Area of Steel) . 1000
Consider Bars to be Provide are of Diameter 8mm.
Therefore, Spacing of Bars = [(π/4) X 82 / 118.53] X 1000 = 424.13mm
Note:- Generally We Provide 200 mm Maximum Spacing Between Bars.

2) At Mid-Span :-

= 87.74 mm2
Spacing of Bars = (Area of One Bar / Area of Steel) . 1000
Consider Bars to be Provide are of Diameter 8mm.
Therefore, Spacing of Bars = [(π/4) X 82 / 87.74] X 1000 = 572.97 mm
Note:- Generally We Provide 200 mm Maximum Spacing Between Bars.

Note:- Calculation of Distribution Steel is Eliminated, Since it is a Two Way Slab.
Step 8 :- Check For Deflection :-
% of Steel = Pt = 100. Astreq / b.d
Therfore, Pt = (100 X 120.1) / (1000 X 101) = 0.11 %
Therefore, Fs = 0.58 X 500 X (120.1 / 251.36) = 138.56 N/mm2
% of Steel Provided = Pt = 100. Astprovided / b.d
Therefore , Pt = (100 X 251.36) / (1000 X 101) = 0.248 %
M.F. = 2.0
Now, dreq= SPAN/B.V.X.M.F = [3151/(26 X 2)] = 60.6mm < 101 mm
As, dreq< dprovided …Safe for Deflection.
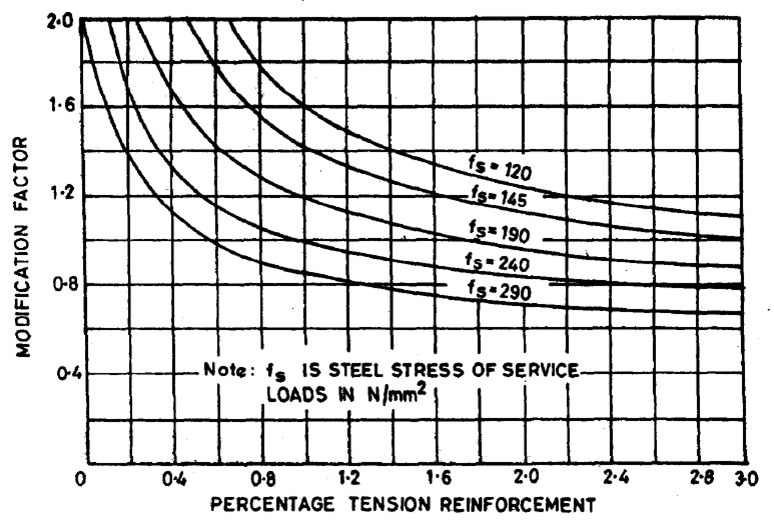
Reinforcement Details :-
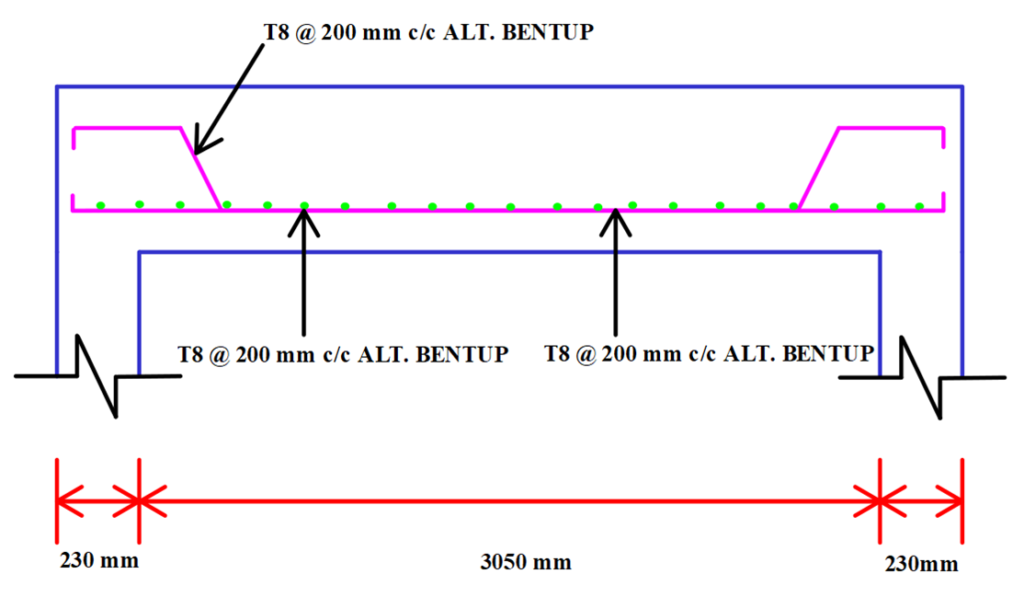
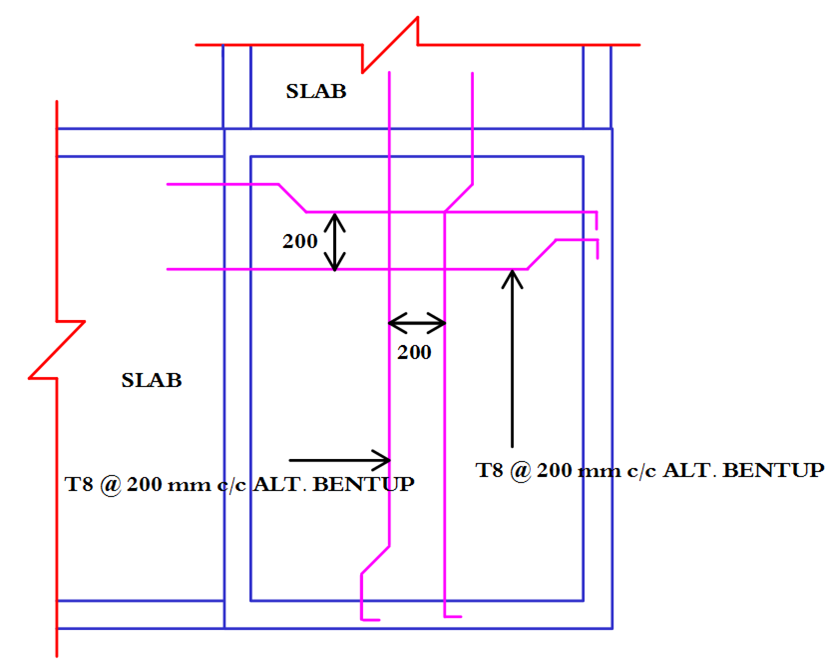